
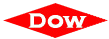




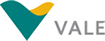





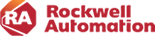

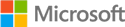


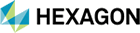


Heavy machinery, such as pumps, motors, and compressors, is critical to the operation of many industries. However, these types of equipment can be prone to failure or breakdown, which can lead to costly downtime and repairs. Predictive maintenance is a proactive approach to maintenance that aims to prevent equipment failure or downtime by regularly monitoring the condition of equipment and identifying potential issues before they occur.
One tool commonly used for predictive maintenance of heavy machinery is vibration sensors. These sensors measure the vibrational activity of equipment and can alert technicians to issues, such as misalignment, bearing wear, or imbalance. By regularly monitoring the condition of heavy machinery with vibration sensors, technicians can identify potential issues before they become serious problems and take corrective action to prevent equipment failure or downtime.
There are several benefits to using vibration sensors for predictive maintenance of heavy machinery:
Overall, the use of vibration sensors for predictive maintenance of heavy machinery can lead to significant cost savings, improved equipment performance and safety, and enhanced asset management. By proactively monitoring the condition of their equipment, organizations can better ensure the reliability and efficiency of their operations.
For further details, please click on ARC’s Vibration Sensor Selection Guide