
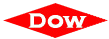




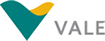





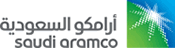

This Additive Manufacturing Selection Guide includes both selection criteria and strategies for choosing the correct additive manufacturing machine supplier.
Additive manufacturing is not just one process, but rather a compendium of different technologies sharing a common philosophy: by building up materials rather than cutting them away, it may become possible to design products with features not economically feasible with traditional design processes. Additive enables and encourages innovation, particularly as the gamut of printable materials continues to expand.
This guide has attributes tailored for industrial organizations, and allows those involved in an additive manufacturing machinery selection process to make quicker and more informed decisions.
Additive manufacturing is becoming mission critical in prototyping and low volume production runs. The selection criteria that impacts users of additive manufacturing ranges from a supplier’s additive process technology and offered build materials to its projected business viability. A supplier’s local and global presence, along with its long-term vision, has a significant effect on the selection process. Other important selection factors for users of additive manufacturing machinery include ease-of-use of the machine, accuracy of the machine, speed of the build process, and quality of the surface finish of the fabricated part. A supplier’s support model, training offerings, and services portfolio are becoming more critical than ever in an era of reduced user in-house staffing levels. [ Learn more about Additive Manufacturing. ]
The following are a few of the strategic issues specifically covered in the Additive Manufacturing Selection Guide:
A principal advantage gained with additive manufacturing capabilities is in the transformation of business strategy and processes. However, companies that are interested in incorporating additive manufacturing into their workflows for the first time often struggle when it comes to introducing the technology in a way that adds immediate benefit but is also scalable.
The quality of any manufactured part is contingent upon the process by which it’s made. For additive manufacturing, this presents a critical challenge. Like molded parts, it’s not just the final shape of the part, but also the bulk properties that are affected by the process. As opposed to machining, the internal structure of an additive manufactured part must be qualified along with external dimensions. Additive manufacturing processes, especially metal-based methods, must also account for thermal stress and warpage when considering the intended geometry of the finished part.
ARC has been researching the Additive Manufacturing market and we know the challenges organization must overcome:
This ARC Selection Guide will help you select the best additive manufacturing system to meet your needs now and in the future.
For more information or to purchase the Additive Manufacturing Selection Guide, please contact us.
Learn more about ARC's Technology Supplier Evaluation and Selection Guides
Learn more about ARC Strategic Services at Advisory Services for Industry Leaders