




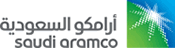

Advanced Process Control includes Multi-variable Predictive Control (MPC) solutions that provide closed loop control and real-time model-based control of a continuous process using empirical or first-principles models. MPC controllers are configured by process engineers and run in the real-time operational environment.
The online optimization continuously monitors the state of multiple processes through a model reference to predict an optimum operation path. Online optimization software typically employs technology for solving simultaneous equations. Presentation of the output of the optimization software may simply be in an advisory fashion to the operator or may directly set a new target to a lower-level control strategy.
Advanced process control includes model-based software that is used to direct the process operation and is commonly referred to as multivariable predictive control (MPC) or model predictive control. These applications require that the process model created accurately represents the process dynamics. Improved economics of the operation or production improvements are typical driving forces for using these applications.
Advanced process control software may include:
ARC analysts maintain an in-depth analysis of the global real-time advanced control and online optimization software markets.