
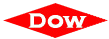




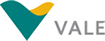





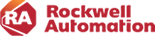

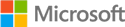


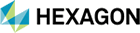


L&T Technology Services leverages its domain expertise, manufacturing processes and R&D knowledge to assist OEMs in technologically advancing their product and solution offerings. With its engineering design and development arm, the company has helped OEMs in adding value in multiple ways through new product development, value engineering, value analysis, product design & design analysis, reverse engineering, CAD modeling & analysis, value added engineering and so forth.
Client Profile: The client is a leading manufacturer of protective packaging products and systems based in North America. As part of its service offerings, the client provides designing and marketing packaging solutions and services for industries worldwide. L&T TS was selected as the engineering partner to optimize their packaging machine design and to achieve significant cost reduction.
Background and Challenge: Air cushion packaging ensures high levels of product protection during transit and storage, and thus the air cushion winder assembly is a critical component of packaging machines. L&T TS as the engineering partner had to identify areas of improvement and ways to optimize the assembly’s design and working mechanism. This inevitably included reviewing and improving the packaging process as well to reduce the overall manufacturing cost.
The value engineering of any product or machine requires a holistic approach taking into account possible trade-offs between performance, cost and production processes. L&T TS had to examine the winder assembly and the manufacturing process to assimilate the number of parts used, reduce material wastage, and optimize assembly weight. This further required reviewing the working mechanism stages and dividing it in sections for further detailed analyses. Based on the working knowledge, L&T TS had to prepare the design specifications including improved layout for sensor mount assembly, motor & clutch.
As part of the redesign, engineering analysis, and part integration process, L&T needed to simulate the air cushion winder assembly mechanism using 3D modeling and simulation tools, and also identify low cost components. Further, the cost reduction, as a result of the part and process optimization, had to be analyzed and executed within the timeframe.
In summary, for the packaging machine assembly the client required:
Overall cost reduction
Weight reduction of the assembly
Improved air cushion production yield
The Solution:
L&T TS provided solutions for value engineering of the packaging machine. They worked on the 3-D part models, drawings, existing component cost, as well as revision of the electrical bill of materials (BOM) to execute the project as per client requirements and standard. L&T TS’s engagement to optimize machine design modifications and leaner manufacturing process included:
Redesign or integration of assembly parts for part count reduction
Weight optimization to sustain required strength and stiffness of assembly and to reduce overall manufacturing cost
Employing engineering design and analysis using 3D modeling and simulation tools such as altium designer 9 for electronic products and systems, and solid works 14 for CAD modeling. Techniques such as finite element analysis were used for alternate low cost part selection of electrical & electronics components
Prototyping of the model
Lastly, verifying the new design, assembly, and working mechanism
L&T TS employed the following cost and quality analysis techniques:
Cost Breakup Analysis for identifying opportunities for cost reduction
Function Analysis system technique for graphically representing the logical relationships between various factors such as components, assemblies, processes, and cost. Furthermore, function cost worth analysis was done as part of value engineering to determine the cost and value of each component function
Fishbone analysis or cause-effect diagram for identifying the possible causes of an issue
Quantifiable Benefits:
With engineering support from L&T TS, the client achieved overall 30 percent cost reduction through machine design optimization and simplification of the manufacturing process. This enabled the client to reduce material wastage and the overall manufacturing cost as well. L&T TS also succeeded in reducing the machine assembly weight to sustain required strength and stiffness of the new assembly. Moreover, with enhancements in the winding assembly and the packaging process, the air cushion yield also improved.
Keywords: 3D modelling, Cost Breakup Analysis, Product Development, Function analysis system technique, Packaging, L&T Technology Services, ARC Advisory Group, value engineering.