
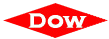




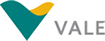





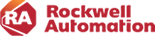

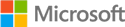


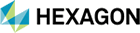


Even before the current global COVID-19 crisis, personnel that work in industrial manufacturing plants and other facilities have needed to be able to monitor or interact remotely with the production operations, often in real time or near-real time. Now more than ever, industry has realized that the ability to have key personnel work remotely is not just a luxury, but in many cases, a necessity. ARC Advisory Group has conducted extensive research to understand the best practices for remote operations in process plants and similar industrial facilities.
Out of necessity, many activities that have traditionally been conducted in person, must now be conducted remotely. In addition to helping enable business continuity in this challenging new age of mandated “social distancing,” ARC research reveals that, in some cases, this has also yielded significant efficiency improvements.
Many of the industry professionals that ARC interviewed indicated that only essential operational personnel really need to be physically present in the control room. This represents a departure from the past, when it was typical practice for maintenance, engineering, and other personnel to visit the control rooms to observe and retrieve the information they needed to perform their work. However, with the personnel safety requirements brought on by the COVID-19 pandemic, plant operations need to protect the process control operators by keeping the number of people in the control rooms at any one time to a minimum.
This increases the need for other key personnel to be able to quickly and easily access appropriate real-time plant and production data remotely.
We asked survey participants which plant operational-related roles needed to be physically present at or near the production line on a full-time or part-time basis. Control room operators were considered essential across all companies interviewed. Some plants also have field operators that are typically required at the production line to perform a variety of operational functions. Where these roles exist, companies typically require them to be available whenever the plant is running. The same is true for maintenance technicians that are frequently required to be physically present to fix or prevent a production equipment problem, often with little or no advance notification.
In these cases, companies have adjusted the physical locations where these personnel work and their proximity to each other. Many we spoke with have gone to great lengths to ensure that the necessary control operators were at safe distances from others. Practices such as installing plexiglass barriers between operator workstations and sanitizing control rooms between shifts have become common practice in many operations today.
Most operations interviewed have not tried to remove personnel completely from the plant operations. Exceptions to this are oil and gas production sites, where unattended operations at the wellhead is normal. Also, some mining operations have been successful in removing personnel from routine activities. All, however, must contend with process or equipment malfunctions. Being able to utilize AI-enabled applications that can predict when something might go wrong allows appropriate personnel to go to the site in a just-in-time fashion from a location near the facility.
Increasingly, digital twin applications are being utilized to enable essential on-site staff still being able to interact with high-fidelity representations of the physical assets to help rapidly troubleshoot and resolve any issues. The digital twin application will inform the on-site operating personnel when an anomaly in the process is detected so that preventive actions can be taken, hopefully before a failure occurs.
ARC Advisory Group clients can view the complete report at ARC Client Portal
If you would like to buy this report or obtain information about how to become a client, please Contact Us
Keywords: Remote Operation, Cyber-secure Networks, Augmented Reality (AR), Digital Twin, Factory Acceptance Tests (FAT), ARC Advisory Group.