
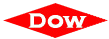




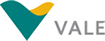





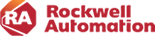

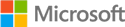


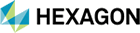


Agnico Eagle Gold Mine, Kittilä, Finland Agnico Eagle, founded 1957, is one of the largest gold mining companies in the world. The Kittilä mine in northern Finland is the largest primary gold producer in Europe. The mine extracts and processes about 4,000 tonnes of ore per day, which results in the production of approximately 200,000 ounces (or 6,000 kg) of gold per year.
The primary chemical used in the separation process is cyanide. Due to its highly toxic nature, highly accurate and reliable pH measurements are required, since an inaccurate or incorrect reading could result in a potentially hazardous situation, delays, and higher costs. Agnico Eagle had previously experienced some problems with its existing pH measurement instruments, including both reliability, functionality, and calibration issues.
The company carried out an extensive year-long field trial with various manufacturers. The process in the Kittilä mine is not an easy one for measurement and analysis devices and there are no simple solutions. Working together closely, teams at Agnico Eagle and Endress+Hauser were able to identify and solve these issues using E+H’s Memosens and Liquiline pH measurement platforms.
The Memosens sensors are designed to perform reliable measurements even in the extreme conditions encountered at the mine. The digital signal between the non-contact sensor and transmitter is not disturbed by any external factors. Calibrations can be performed more conveniently, and Agnico Eagle found that the automatic cleaning feature provides measurable improvements in efficiency and staff morale, since it avoids the need for technicians to perform the difficult, time consuming, and inconvenient cleaning procedures outdoors, especially during the cold Finnish winter.
Agnico Eagle Gold Mine
E+H’s Memobase Plus calibration diagnostics and lab measurement software allows sensor data to be transferred to a PC via a USB port, providing instantaneous access to the sensor condition and diagnostics information. According to Agnico Eagle personnel, the installation resulted in a 90 percent reduction of time spent on calibrations and field repairs (from 20200 to approximately 240 labor hours per year). Chemical consumption was reduced by up to 50 percent. And the ability to use the same measuring technology for manual and inline measurements improved data consistency and confidence in these critical measurements.
“Reliable pH measurement allows us more precise dosing of chemicals and therefore substantial cost savings.” Annika Niiranen Metallurgist, Agnico Eagle