





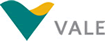

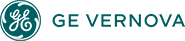









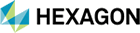


Decreasing oil prices, expanding supply, and new regulations are bringing significant technological changes in the oil & gas industry. To stay competitive, the petroleum sector is undertaking a digital transformation and turning to Big Data, Industrial IoT, and advanced analytics to unlock business value. For Royal Dutch Shell, the journey to industrial analytics began several years ago when the company decided to maximize the value of its data.
In a recent ARC Industry Best Practice Digital Transformation Council webinar, Peter van den Heuvel, Product Manager Real-Time Data at Shell, discussed how the company takes process data to the next level by utilizing the Cloud, smart applications, and advanced analytics. Robbert Kroes, Enhanced Problem Solving Team Lead at Shell, then provided examples of use cases where Shell has realized insights and benefits from its approach.
For over two decades, Royal Dutch Shell has harnessed the power of digital transformation to optimize its operations and drive enterprise-wide performance. Shell gathers operational data from over 10 million devices across its enterprise, located from the Gulf of Mexico to Australia’s Browse Basin. Every piece of industrial equipment, from drill bits miles beneath the ocean floor to the flares of its refineries, is monitored by Shell’s OSIsoft PI System, one of the largest of its kind in the world.
Early on, Shell realized that it needed to empower its engineers to achieve the company’s enterprise-wide objectives. The enormity of the data Shell generates is impressive. In September 2020, for example, 12 million events per second were monitored and 500,000 real-time calculations were made every minute, with 50,000 operational data displays available every day. Ten million instruments or measurement points are typically measured, and 30,000 reports are generated daily for 25,000 users. Shell has 25 years of data available online in the PI System. All Shell’s businesses – upstream, midstream, and downstream - are connected to the PI System. These include unconventional energy resources and windfarms, along with other renewable generation assets. The data in Shell’s PI System increased from one million events per second in January 2017 to 12 million events per second in September 2020.
Mr. van den Heuvel, stressed the importance of both having high-quality data, and then transforming this data into actions. For Shell, the problem was that with 12 million real-time data events, this can be like “looking for a needle in a haystack.” Without trustworthy, high-quality, in-context data and information, users cannot make good decisions or take data-driven actions. By democratizing sensor-based data across its global enterprise, Shell is empowering employees with smart applications as it advances towards the future of advanced analytics and AI. Shell is also making the data available for cloud applications, digital twin initiatives, and other smart applications.
A few years ago, Shell started working with Seeq to create self-service analytics. Today, all company data is accessible to the process engineers, scientists, and subject matter experts via its Seeq advanced self-service analytics tool with machine learning. According to Mr. van den Heuvel, as a trusted partner, Seeq is reading 350 million events every day from the company’s many PI Systems around the world.
Shell uses a single SaaS deployment for its global users because this provides new updates and features every few months, with greatly improved user accessibility. Seeq is installed in a server, and the company maintains the Microsoft Azure-based SaaS platform (Seeq is a Microsoft partner). The data is growing rapidly as Shell continues to discover new use cases for the application.
Using a combination of monitoring and descriptive, diagnostic, predictive, and prescriptive analytics, Seeq empowers users to determine what is happening now, why it happened, what happened in the past (and why), what will happen, and what should happen. This is allowing Shell to move from reactive to proactive operations.
Seeq makes it easy for users to cleanse and analyze the data using capsules that quickly highlight any data abnormalities. Seeq also provides visibility into changing trends like temperatures or pressures. Mr. van den Heuvel mentioned that, in one refinery, Seeq was able to analyze data in 30 minutes, a task that used to take its workers four months using Excel.
Seeq accesses and cleanses the data from the PI system, leaving the data in place. The Seeq database now includes hundreds of formulas built for Shell’s users. Shell representatives provided several examples of how this solution helps solve challenges across the company.
Robbert Kroes, Enhanced Problem Solving Team Lead at Shell, described a use case in which the self-service analytics were used to gain valuable insights on the company’s large, Prelude floating natural gas (FLNG) vessel. This vessel operates in remote corners of the world, often over 200 kilometers from the nearest shoreline.
Because of the remote location, it is important that everything is done right the first time since there is no room for error in the production process. The challenging logistics limit what Shell’s multi-disciplinary engineering team can do. As a result, they would rather use more data for any analysis to be sure that users make better decisions and do the right things. Shell has been collecting a lot of data on the Prelude FLNG, which is available to its office in Perth, Australia.
One of the benefits of producing energy offshore is that plentiful seawater can be used to cool the utilities. This is done by pumping the seawater through the heat exchangers, which is then discharged back to the sea. The problem is that the process creates an opportunity for marine life to develop inside the heat exchanger. Some of the smaller organisms, shells, and larvae from the sea settle on the heat exchanger plates and filter (see photos). The buildup of the marine life causes a pressure drop, leading to problems with the pumps and reducing heat exchanger capacity. Cleaning every plate in the heat exchanger would be a massive undertaking. Shell overcomes this problem by chlorinating the system, preventing the marine life from settling. The chlorine is generated by splitting seawater (NaCL + H20) into hydrogen and hypochlorite (NaOCL) using an electrolizer.
Ideally, the team wants to minimize the impact on the environment by releasing the smallest practical amount of chlorine (typically less than found in tap water). According to Mr. Kroes, “This is a narrow operating band where we want to make sure the chlorine is sufficient to eliminate the marine life problem, but also minimize the discharge of chlorine into the sea water.”
One of the challenges for injecting enough HCl was the scale built up in the injection lines and valves. The Shell team analyzed the mechanism behind these blockages by analyzing the available data using Seeq. The team looked at the velocity of the flow and thought that the problem was the result of velocity dropping below a certain scaling threshold.
The first issue was to demonstrate that the low flow rates were actually causing the issue. The data revealed that the system had low and high flow rates at different times, and that trending the data was not sufficient to determine the flow rate or scaling threshold.
The problem was determining the amount of liquid delivered to the system at the lowest flow velocity at which solids drop out of the solution, or keeps small scales in suspension, to prevent further scaling.
Initially, the team members calculated the velocity in every line to determine the discharge velocity at every injection point, and then back calculated the flow per line. Then, using the system’s geometry, they calculated the velocity. The next steps were determining the:
Using the deposition velocity and the variable velocity in every line, the team used the analytics software to compare the velocities in the system to determine the scaling position. When the actual velocity was lower than the threshold, the scale particles were more likely to be deposited. This provided the specific flow rates and volume of solids that would put the system at risk for scaling. While it was obvious that the velocity was causing the valve scaling, the data revealed a different cause for the low velocities than initially thought. Ultimately, the team determined that they needed different valves, so these are being changed to an improved design to avoid future blockages.
To minimize the impact of the environment, the next step was to determine the minimum volume of chlorine that needed to be injected into the seawater system to make the marine microorganisms inactive.
The team discovered that they had not been measuring the actual amount of chloride correctly. While the initial curve looked normal, when they stopped the chlorine injection and waited six hours, they observed the chlorine analyzer continued to show significant concentrations of chlorine. An analysis revealed that this was due to the chlorine analyzers operating below their designed operating range. This was corrected by changing the system to show zero concentrations when the measurements are below the analyzers’ operating range. This enabled the team to shift the operating point to get positive confirmation that they are injecting sufficient chlorine to inactivate microorganisms, but not at high enough levels to impact the environment.
Shell has collected over twenty-five years of data, creating one of the world’s largest operational data stores. As shown in the FLNG case study example, the company is moving away from traditional spreadsheet approaches for data analysis. Shell is now using Seeq’s advanced, self-service data analysis software to better leverage its vast data store. This provides them with the ability to make data-driven decisions to help solve problems better and faster. Mr. Kroes commented that Seeq’s extensive toolkit with predefined functions is a key differentiator over other solutions.
Based on ARC research and analysis, we recommend the following actions for owner-operators and other technology users:
ARC Advisory Group clients can view the complete report at ARC Client Portal
If you would like to buy this report or obtain information on how to be-come a client, please contact us
Keywords: Sustainability, Business Continuity, Advanced Analytics, Shell, FLNG, Real-time Data, Seeq, OSIsoft, ARC Advisory Group.