





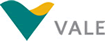

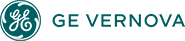









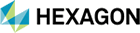


The Industry of Things World Asia event, organized by Berlin-based we.CONECT, returned to Singapore this July. As indicated by its title, the event focuses on the industrial strand of IoT, making it an attractive forum for delegates from manufacturing industries and for technology suppliers to the sector.
As with the two previous editions of the event in 2017 and 2018, the high percentage of end user presentations provided a wide variety of real-world, cross-sector industry case studies and viewpoints. These include electronics, steel, pharmaceuticals, machine building, chemicals, oil & gas, and aerospace.
ARC Advisory Group research indicates that end users are often challenged to articulate the business case and financial justification for Industrial IoT-related projects. These can represent a significant hurdle for companies adopting Industrial IoT technology or embarking on broader digital transformation journeys. Thus, the opportunity to learn from other end users on their motivations, experiences, and challenges can be invaluable for industrial companies looking to initiate and move forward with their own projects in these areas.
In addition to the typical presentations, this year’s Industry of Things World Asia offered delegates a mix of learning and networking opportunities.
A series of “Industrial IoT Bootcamps” on the first day explored several different topical Industrial IoT themes, applications and constituent technologies. These included how to justify new IoT projects, cognitive approaches to maintenance, ecosystem collaboration, developing a roadmap to Industry 4.0, and the advantages of OPC UA for systems integration.
Informal “Icebreaker Round Tables” at the evening cocktail hour also allowed delegates – beverage and canapes in hand – to interact with experts discussing pertinent Industrial IoT topics such as productivity improvements and new revenue streams from digital manufacturing transformation; data governance and policies; pillars of Industry 4.0 transformation success; and industrial cybersecurity in a hyperconnected world. ARC helmed the industrial cybersecurity round table. Issues introduced and discussed with delegates included the widening attack surfaces from increasing IoT connections; the need to pay proper attention to securing IoT endpoints; threat intelligence and vulnerability assessments; and IT/OT roles and responsibilities in industrial cybersecurity.
While there were no cappuccinos or cakes on offer in the World Café conference on the final day of the event, this segment provided plenty of food for thought. The World Café is a we.CONECT initiative where delegates are brought together to discuss issues, share challenges, and gain new perspectives in sessions moderated by an expert speaker.
In the World Café session, Avoiding Digital Transformation Stalls and Developing a Strategy for Success, Mick Mancuso, director, Connected Enterprise Consulting, Rockwell Automation, discussed the importance of understanding where a company is in terms of digital maturity as it journeys toward the goal of transformation and deploying suitable tac-tics at different stages of that journey.
Mr. Mancuso outlined five stages:
With more than 30 end user presentations at this year’s conference, delegates had plenty of opportunity to learn about the business drivers, implementation challenges, and benefits of Industrial IoT and digital transformation from companies already at the frontline. The experiences articulated by three companies from quite different industrial sectors follow.
Data storage systems manufacturer, Western Digital, has more than 70,000 employees around the world and multiple production sites, predominantly in Asia. The company’s impetus for embarking on its SMART Factory initiative was the desire to become “a data- and insights-driven business” to achieve performance improvements in quality, asset utilization, labor efficiency, and cost. As presenter Philip Bernard, vice president of global hard disk drive (HDD) operations & engineering, outlined, operational realities in its manufacturing include high product complexity (250 components make up the typical hard drive), long cycle times, and high unit volumes.
Western Digital used a highly structured approach for its SMART Factory initiative. This comprised several stages:
To accelerate adoption and acceptance, the company used the Mini-mum Viable Project (MVP) approach: Think Big − Start Small − Scale Fast.
One example of SMART Factory success is the implementation of a real-time machine learning-based test process. This predicts which HDDs are likely to pass product test and so can go through a simplified test process, and which are likely to fail and hence require regular full testing.
The Adaptive Test Process led to savings on the order of millions of dollars a year by improving test equipment utilization and product quality. This project also helps illustrate Western Digital’s MVP approach in action:
Shaun Gregory, executive vice president and chief technology officer at Woodside, Australia’s largest natural gas producer and a pioneer of the LNG industry in the country, echoed Western Digital’s approach to digital transformation in his presentation about the company’s adoption of IoT and artificial intelligence: Think Big, Prototype Small, Scale Fast.
To start, make sure you’re working on a big problem, said Mr. Gregory, because there’s a risk in deploying new technology and that risk must be worth it. “So, think big, because if what you’re planning is going to make a 1 percent improvement to cost, I am not interested. But if you say you’re going to halve my cost, you have my attention – and some seed funding.
“Prototype small is about telling people to stop writing business plans and give it a go – quickly and at low cost. And because you lower the consequence of getting things wrong, as long as you’ve learned something, I don’t really care if you fail. Once you have a working prototype, if you do not scale this into your business, you won’t reap the benefits you anticipated.” Mr. Gregory admitted that scaling solutions is the aspect the company has struggled with the most.
One IoT prototype project he described took place in a water treatment plant section of an LNG complex. The project involved a pump with a visual oil level indicator. Previously, a staff member had to trek out to the plant, located in a remote area subject to temperatures of 40 degrees C; note the oil level; and enter the value once back at the PC.
Rather than go to the expense of retrofitting the equipment with a digital sensor, Woodside now uses a camera to take a photo of the indicator level at one-hour intervals. The data goes to the IoT cloud where a machine learning algorithm determines the percentage oil-fill level and the value is displayed on the digital twin representation of the plant.
This eliminates the uncomfortable, time-consuming, and non-value-adding steps of manual check and data entry. And, importantly, as Mr. Gregory pointed out, the project increases workers’ awareness and builds confidence in new technology, making it easier to successfully scale to other applications and other parts of the LNG complex. As a non-hazardous area, the water treatment plant was specifically chosen for the prototype project to lower the consequence of failure.
ARC Advisory Group clients can view the complete report at ARC Client Portal
If you would like to buy this report or obtain information about how to become a client, please Contact Us
Keywords: Industry of Things World Asia, Industrial IoT, Industry 4.0, Digital Transformation, Rockwell Automation, Comfort Systems USA, Western Digital, Woodside, ARC Advisory Group.