





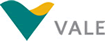

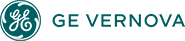









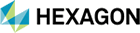


With ever increasing competition, tighter margins and growing consumer demand for more personalized products, it’s no surprise that the industry is continuously searching for the next big competitive advantage. This is precisely where digital transformation and the industrial internet of things (IIoT) offers tremendous opportunity, especially if the IIoT operational architecture is done right. With a broad range of use cases including remote monitoring and diagnostics for asset reliability, advanced energy management, production performance and quality improvement, it’s clear there are some impressive benefits to be gained.
That said, many industrial companies are struggling to advance these digital efforts. In my experience, these issues often stem from the pure hype of the IIoT and the need to “do something”: businesses recognize that they should transform, but they don’t often know how, what areas to target or even where to start.
This typically results in no action at all or a rash of seemingly random or even hastily-assembled pilots or Proof of Concepts (POCs) designed to demonstrate some level of progress against corporate objectives. The most successful implementations we’ve seen are based on solid business directives (target areas) that take a very open and comprehensive approach to addressing digital transformation that is grounded in some very pragmatic and well-thought out action plan.
A good first step is to determine what areas of the business stand to benefit the most. Two major areas of focus we see today include optimizing profitability associated with the production value-stream (think “making stuff” or the production side). The other is maximizing the return on assets and capital deployed (think asset reliability, maintenance and performance).
Going one level down, it’s important to target some specific areas within the operating areas of the business – once again – based on where you seek to improve. For example, do you need to improve quality? Increase yield? Boost performance or productivity? Or increase margins? The point is to identify the levers needed to drive the business based on market dynamics. Identifying the target areas requiring improvement is the first step. Following that, a new operational architecture can be determined.
You can think about the operational architecture as the “scalable, stable and harmonized framework” that supports your corporate strategies. Once these business objectives and an operating architecture is determined, an investigation into different approaches and technology “enablers” can be performed. This can be a confusing and complicated process thanks to the hype of all things IoT and digital. To better navigate this process, companies should stay grounded in the objectives and how these enablers can be applied.
One area of considerable hype – but also considerable value realization – is the IIoT. With unprecedented access to real-time and historical process and production data, companies can access and make use of information from new systems and sources that were previously too expensive to instrument or otherwise disconnected. Don’t get me wrong, most customers we see have more than enough raw data – but it’s typically stranded and/or out of context, unreachable or insufficient. By organizing and contextualizing existing data – and then extending and augmenting with the help of IIoT devices, you can realize significant gains.
Examples include stranded assets or equipment in remote locations or not “wired” in to PLCs or RTUs; these can now be reached via new wireless protocols and low-cost sensors. New data sources from existing equipment can be accessed via “shadow” or secondary sensing, providing temperature, vibration and other information. Once this data is collected and consolidated, advanced capabilities can then be applied to drive productivity to those targeted business areas. For example, new gains in performance can be had by better tracking and managing stoppages; additional sensors feed advanced analytics to identify and prevent catastrophic failure. These data sources are certainly important – but they are merely a feed to the advanced applications/solutions.
If the IIoT is one of the key building blocks of digital transformation, the cloud is the second critical component. The cloud is so valuable in implementing digital transformation because it enables unprecedented commercial and technical flexibility. With the cloud, businesses can essentially configure, provision and design exactly the solution they need, when and where they need it. Think of the IIoT as a set of studio microphones capturing and contextualizing all the sound within a room. The cloud is the mixer, combining and amplifying the right pieces of music to create a symphony.
Migrating to the cloud comes with its own set of decisions over what should move to the cloud, and what should stay on-premises. Here, as with the IIoT, it’s important to remain focused on the business objectives. It doesn’t do anyone any good to just jam everything into the cloud. There needs to be a reason, such as better access across your organization, or an easier, more secure way to share data with suppliers or partners. For instance, there are many good reasons to keep HMI/SCADA systems on-premise. But, it may make sense to host predictive maintenance or OEE monitoring capabilities in the cloud.
Rob McGreevy, Vice President of Operations, Information and Asset Management at Schneider Electric, is responsible for the Operations, Information and Asset Management software business globally. This includes responsibility for defining and executing the software product and business strategy. The business Rob supports focuses on industrial information management, including enterprise data management, IIoT, cloud and mobile applications; operations management including manufacturing execution and manufacturing operations management technology; and asset performance management, including predictive analytics and integrated EAM capabilities. Rob comes to Schneider Electric with 20 years of experience working in the software business with a focus on manufacturing and industrial applications.