





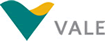

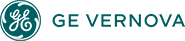









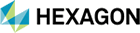


Founded in 2016, Swedish battery-maker Northvolt’s manufacturing facilities have the goal of producing “green” batteries – power cells made mostly from recycled batteries. The company employs a “cloud-first” strategy of connected factories that share information in applications, such as detailed product traceability, near-real-time monitoring of manufacturing line effectiveness, computer vision powered defect detection, and machine learning (ML) and artificial intelligence (AI) modeling to predict quality and performance of the produced battery cells.
Northvolt uses a “Cloud Factory Module” design, a modular cloud-based architecture. Each module represents one building at a connected factory site, represented by a single AWS account. The design makes it easy to start up a new factory environment or extend an existing factory with new buildings. According to the company, the model improves the security posture, which helps to ensure business continuity if a faulty change is implemented. Software can be released into different parts of the factory using blue/green (staging/live) and canary (incremental) deployment strategies.
Each factory maintains its own data account where raw data are transformed and prepared for reporting, analytics, research, and ML applications. Any factory software components not specific to a single building are deployed into a core account. Critical infrastructure not tied to a single factory is managed globally. The networking layer that will host the transit gateways, firewalls, Direct Connect, and other infrastructure lives in its own network account. The global and shared accounts include infrastructure for observability, shared Amazon Elastic Container Registry (Amazon ECR)—a fully managed container registry—and global front-end apps that are needed to run our factories.
The Cloud Factory Module design allows quality engineers to flag nonconformities in battery cells around the clock. In addition, it makes software updates performed during factory operations undetectable by engineers and technicians. According to the company, key design requirements are redundancy, reliability, security, and scalability. Northvolt plans to use the Cloud Factory Module design as a digital blueprint for future factories.
Northvolt Ett factory uses Amazon Kinesis Data Streams, a serverless streaming data service that makes it easy to capture, process, and store data streams at virtually any scale. The company anticipates ingesting hundreds of thousands of records per second, which will serve both a short-term hot data path for near-real-time applications and long-term storage in an Amazon Simple Storage Service data lake for subsequent larger data jobs with data built tool and Apache Airflow.
So how do data get pushed into the cloud? Across any given factory, Northvolt plans to have thousands of Linux-based gateways as part of multiple massive Kubernetes clusters managed in AWS using Rancher. Each machine on the factory floor is mapped to a high-availability pair of gateways. The production machines push their data into Kinesis data streams that are mapped per area within the buildings of the factory. From here, AWS Lambda, a serverless, event-driven compute service, and Amazon Kinesis Data Firehose manage the dataflows into the hot and cold data paths.
The Cloud Factory Module design allows Northvolt to be scalable and flexible in way it manages different factory architectures using AWS. This design also helps to push different releases of software into different parts of the factory using blue/green deployments, like with regular web application, with virtually no downtime.
According to Northvolt, using AWS helped the company to be scalable and flexible to design, build, and operate its own factories on its journey toward building the world’s “greenest” battery.