





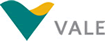

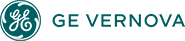









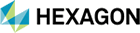


Eight years ago, BASF’s Monomers strategic business unit began a journey to improve its supply chain’s reliability. The company had been experiencing frustrating problems with its bulk trucking shipments, resulting in late deliveries and unhappy customers. The company’s trucking companies were also experiencing similarly frustrating (and related) problems around route optimization and poor asset utilization. In response, BASF created a collaborative “Bulk Trucking Symposium” and implemented technology to improve the situation for BASF, its customers, and its carriers. BASF wanted supply chain excellence.
BASF has been using a real-time visibility solution from MacroPoint, a Descartes company, to improve its own delivery reliability as well as the productivity of the transportation providers the company uses to service its North American market. But implementing good technology is not enough. Getting the most out of software also requires dealing with internal and partner cultural issues and improving processes. According to Bill Wehrle, the Director of Supply Chain for isocyanate and inorganic chemical products in BASF’s Monomers business unit, the company’s current journey to improve its supply chain’s reliability started eight years ago.
Mr. Wehrle spoke at Descartes’ Evolution user conference in March. BASF Corporation, a chemical company headquartered in Florham Park, New Jersey, is the North American affiliate of BASF SE, of Germany. BASF has more than 17,500 employees and sales of over $16 billion in North America.
ARC Advisory Group clients can view the complete report at ARC Main Client Portal or at ARC Office 365 Client Portal
If you would like to buy this report or obtain information about how to become a client, please Contact Us
Keywords: BASF, Real-time Visibility, Continuous Improvement, Collaboration, ARC Advisory Group.