





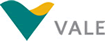

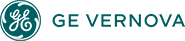









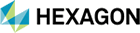


Artificial Intelligence (AI) will fundamentally disrupt not only the way we produce, but also the way supply chains look like. In 10 years, 30- 50 percent of manufacturing process will use AI, which will be increasingly embedded.
Now, we are in the middle of the transition and there are many use cases that show how to implement AI successfully. There are many lessons learned from these case studies. One of the key takeaways is that 90 percent of all work in an AI project is not actually about AI, but is done around it, this includes cleaning data, organizing teams, restructuring, bringing stakeholders together, and much more. Looking more at the technology, successful implementation often is based on a microservice architecture. This allows for faster deployment and project completion times as well as effective lifecycle management of AI -- something that should always be incorporated right from the beginning.
The key challenges across the lifecycle include:
This strategy report provides not only a detailed analysis of this key challenges, but also the key solutions and strategies to avoid them altogether. This strategy report summarizes the discussion and learnings from 2 events in early 2021, where ARC held a Forum workshop as well as an online discussion. Companies that supported these events include IBM, Microsoft, NNaisense, Pfizer, Philip Morris, Phoenix Contact, Siemens, and Voith.
Use cases enable us to see beyond theory and expand our thinking to include real-life problems. These may include mundane things such as differences in time zones, travel restrictions of experts, or even point us to fundamental challenges in AI.
Microsoft shared how they provide the backbone for many operations. The vision ranges from device to the ERP level, creating a seamlessly connected factory. KPIs improvement shared ranged up to 200 percent, averaging between 50-100 percent. It was also critical to see that these improvements addressed productivity, sustainability, agility, speed to market, as well as customization. The latter demonstrated to thing: Without AI, there will be no batch size 1 with the KPIs close to mass production.
IBM shared use cases for a cognitive supply chain, which adapts to disruptive events as well as changes in the company processes, and how they achieved it. Disruptive events include not only pandemics, but other economic and natural threats from the bursting of economic bubbles to flooding, volcanoes, and other extreme weather or climate-related events. A successful and resilient supply chain needs to be able to react quickly to these “black swan” events. AI is certainly not the weapon of choice for all supply chain events, and there are ways to determine if AI is right for you. IBM makes the decision using a 4-field matrix along the axis Frequency (exceptional to regular) and Complexity (rules based to situational). AI is most effective in regular events, which are rather complex, where there is a sufficient amount of data and AI can adapt to complex situations (see chart). This segmentation is based on IBM’s own experience, using AI in their supply chain. Use cases include:
Siemens shared in detail its AI use case for electronics manufacturing quality inspection. One of the most important points presented in this use case was that “AI models won’t age like good wine.” As data drifts during production (different temperature, quality and characteristics of input material, machine wear) AI models need to be retrained and continuously optimized. This is also true for any structural shifts, like product changeover or change in desired outcome. While the case study on quality is certainly specific, the learnings are generic and are valid for almost all applications. One of the key learnings is that AI needs a concept for the lifecycle right from the start. Siemens approaches this by integrating AI monitoring components into the productive workflow and micro-service architecture. Features include:
Phoenix Contact uses its own production processes as a real-life testbed for new technologies. This provides many benefits, including working with real-life data to see if something works only on paper or also in real life, and of course continuous optimization of operations. Key in this process is the feedback loop between the data analysis and the production team. Phoenix Contact uses the insights gained from AI to retrofit existing assets, integrate new assets, and to design future assets more intelligently. This all done on a microservice based architecture, which enables:
Phoenix Contact also has close collaboration with universities. This approach certainly takes a bit more time and more internal resources than simply outsourcing it to an AI specialist, but it also enables a deeper understanding of how AI works – both its capabilities and its limitations. When a company wants to offer its experience to clients afterwards, collaborating with colleges and universities is a good strategy. One of the key achievements was that through the sound understanding of the process, Phoenix Contact was able to use only 3-5 percent of all IO signals to achieve the required outcome. This means that the amount of data (with all the additional work and cost associated) needed can be quite small.
Pfizer provided us insight into their current transformation process, featuring examples with Natural Language Processing for maintenance. Pfizer’s approach to AI in manufacturing is interesting for several reasons:
The information shared focused on two aspects: lower costs, and the ability to deliver product on time. Time to market is key for a pharmaceutical company and can make or break the profits, as R&D costs rise consistently and the timespan to monetize on a given product is shrinking globally. AI is used in a framework that fits the IBM classification of complex/situational and regular. In this case, the technology used was NLP (Natural Language Processing) combined with topic modeling. During our session, Pfizer also talked about the size of the team necessary, for a company with almost 100,000 employees, it was a small team of far less than 20 people.
ARC Advisory Group clients can view the complete report at ARC Client Portal
If you would like to buy this report or obtain information about how to become a client, please Contact Us